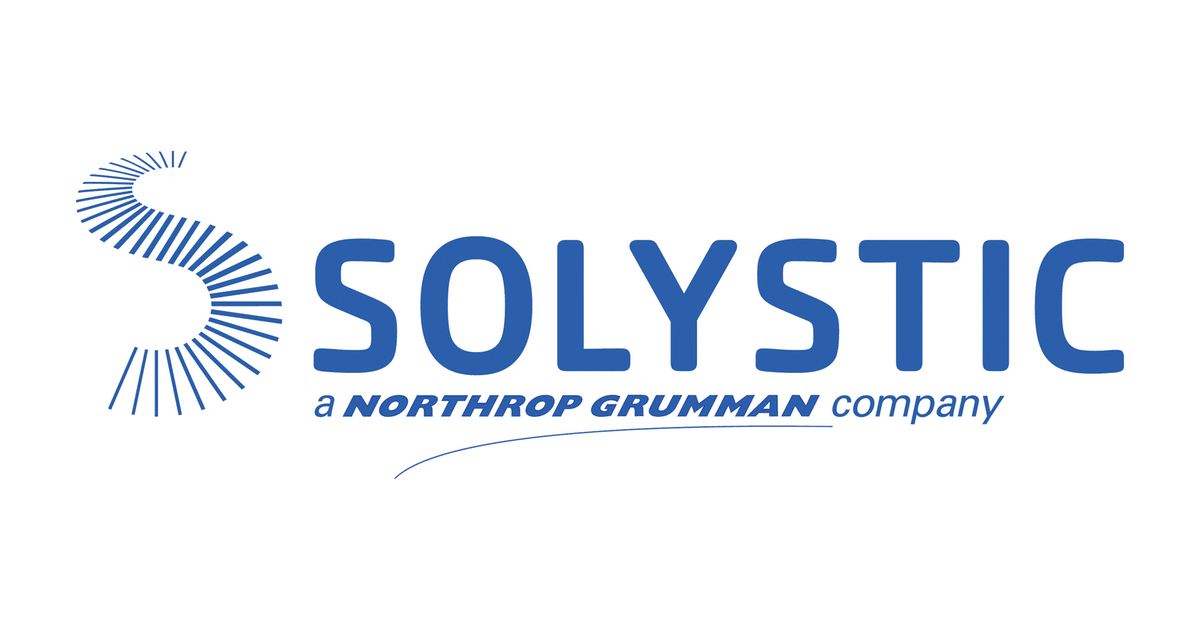
improves its spare parts service with AZAP
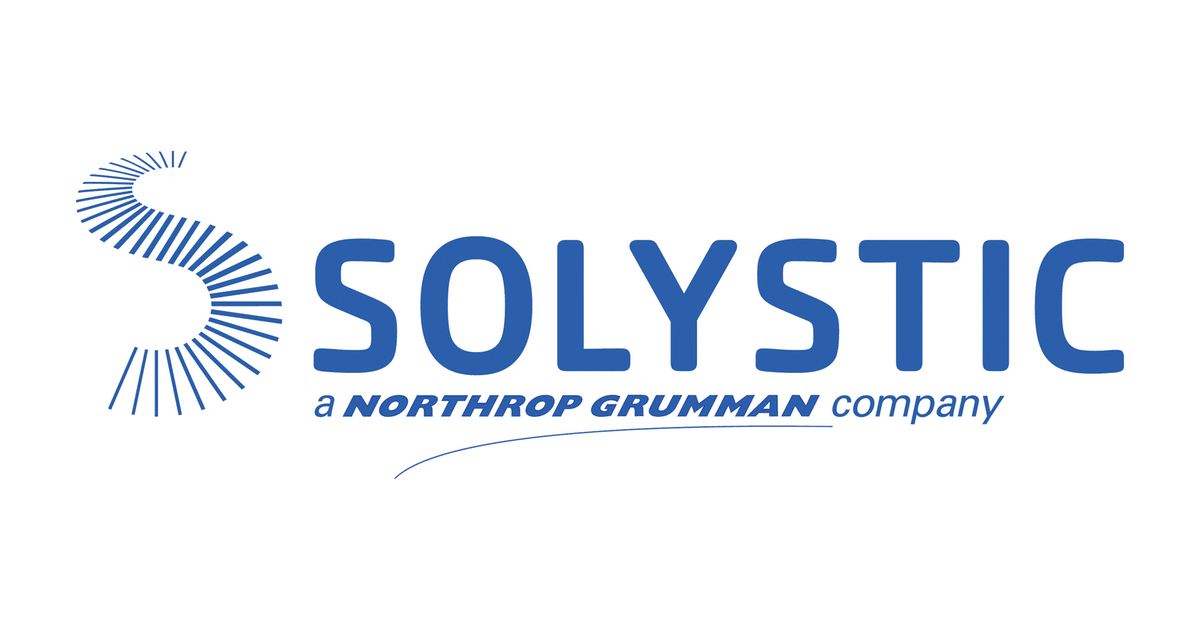
improves its spare parts service with AZAP
Born in France in the 1950s, SOLYSTIC provides solutions for the identification, tracking, sorting and delivery of objects to major operators in the postal industry, e-commerce and distribution. Present in 25 countries, it belongs to the American group NORTHROP GRUMMAN COMPANY and achieves a turnover of 100M €. It is responsible for technical support, the supply of spare parts and the maintenance of its machines.
Sales forecasts by customers
In a context of a growing market but demanding in terms of deadlines and machine availability (penalties in the event of stoppage), SOLYSTIC has launched a project to better meet the contractual deadlines for the provision of its spare parts (PR), while controlling its stocks. To better anticipate his needs, he decided to establish forecasts by customer. Its goal is also to improve its service rate and administrative productivity, as well as to offer new services to its customers.
An IS unreliable, heavy and not sustainable
The Spare Parts and Repairs Service (S2R) manages supplies in France from a central warehouse (M101), and in England for Royal Mail from the MSSF platform. At the IS level, SAP managed supplies for M101 and MSSF while consumption forecasts were prepared each month under Access. This system posed problems of reliability, cumbersome updating, risk of errors and maintenance over time.
Prior classification of PRs by AZAP
After consulting the market, SOLYSTIC selected AZAP. A large preliminary work of classification of the PRs with adapted forecasting and inventory management policies was carried out with AZAP in April 2015. Of the 28,000 PR references in the database, 800 sold more than 3 times the previous year made the difference. ‘object of a forecast calculation and safety stocks by AZAP, 5,200 being managed manually and 800 erratic having a safety stock. This classification, initially global, had to be broken down by site.
Revenue gains
The AZAP solution, operational in May 2016, achieved the expected results in qualitative and quantitative terms, allowing SOLYSTIC to gain turnover through customer loyalty and an extension of its export services …
SOLYSTIC in brief
- Provider of solutions and services for the courier and parcel industries
- 100 M € turnover, 80% of which is exported
- 30 international operators customers
- more than 500 employees
- 3 sites: Paris (head office), Valence (production), Kontich (maintenance)
- 28,000 PR stored on 2 sites
Project challenges and objectives
- Respect the contractual deadlines for the provision of spare parts while controlling stocks
- Gain administrative productivity
- Develop / share the same forecast repository between the different internal stakeholders
Modules
- AZAP Demand Planning
« Azap helped us a lot in the article classification process. We now control our stocks through the monthly analysis given by AZAP in a context of strong growth. We have also significantly reduced our breakdowns and are ready to extend our maintenance services to other customers by developing other local export storage sites. »
Christian Zahm,
Head of Spare Parts and Repairs – SOLYSTIC
Born in France in the 1950s, SOLYSTIC provides solutions for the identification, tracking, sorting and delivery of objects to major operators in the postal industry, e-commerce and distribution. Present in 25 countries, it belongs to the American group NORTHROP GRUMMAN COMPANY and achieves a turnover of 100M €. It is responsible for technical support, the supply of spare parts and the maintenance of its machines.
Sales forecasts by customers
In a context of a growing market but demanding in terms of deadlines and machine availability (penalties in the event of stoppage), SOLYSTIC has launched a project to better meet the contractual deadlines for the provision of its spare parts (PR), while controlling its stocks. To better anticipate his needs, he decided to establish forecasts by customer. Its goal is also to improve its service rate and administrative productivity, as well as to offer new services to its customers.
An IS unreliable, heavy and not sustainable
The Spare Parts and Repairs Service (S2R) manages supplies in France from a central warehouse (M101), and in England for Royal Mail from the MSSF platform. At the IS level, SAP managed supplies for M101 and MSSF while consumption forecasts were prepared each month under Access. This system posed problems of reliability, cumbersome updating, risk of errors and maintenance over time.
Prior classification of PRs by AZAP
After consulting the market, SOLYSTIC selected AZAP. A large preliminary work of classification of the PRs with adapted forecasting and inventory management policies was carried out with AZAP in April 2015. Of the 28,000 PR references in the database, 800 sold more than 3 times the previous year made the difference. ‘object of a forecast calculation and safety stocks by AZAP, 5,200 being managed manually and 800 erratic having a safety stock. This classification, initially global, had to be broken down by site.
Revenue gains
The AZAP solution, operational in May 2016, achieved the expected results in qualitative and quantitative terms, allowing SOLYSTIC to gain turnover through customer loyalty and an extension of its export services …
SOLYSTIC in brief
- Provider of solutions and services for the courier and parcel industries
- 100 M € turnover, 80% of which is exported
- 30 international operators customers
- more than 500 employees
- 3 sites: Paris (head office), Valence (production), Kontich (maintenance)
- 28,000 PR stored on 2 sites
Project challenges and objectives
- Respect the contractual deadlines for the provision of spare parts while controlling stocks
- Gain administrative productivity
- Develop / share the same forecast repository between the different internal stakeholders
Modules
- AZAP Demand Planning
« Azap helped us a lot in the article classification process. We now control our stocks through the monthly analysis given by AZAP in a context of strong growth. We have also significantly reduced our breakdowns and are ready to extend our maintenance services to other customers by developing other local export storage sites. »
Christian Zahm,
Head of Spare Parts and Repairs – SOLYSTIC
Results obtained
Qualitative
- Team reorganization
- Clear sharing of responsibilities
- More reliability in exchanges
- Help with stock reinforcement
- Ease of having ABC curves in quantity and cost
Quantitative
- Reduced delivery times
- Control of the stock level
- Increase in turnover thanks to the better availability of parts (customer loyalty)